In an ever-changing world, stability and reliability in logistics are more critical than ever. SAP Extended Warehouse Management (EWM) offers the perfect solution to streamline logistics operations. In this series of articles about SAP EWM we will explore its various facets and how they enhance operational efficiency. We will start with EWM’s fundamental functionalities: the Inbound Process.
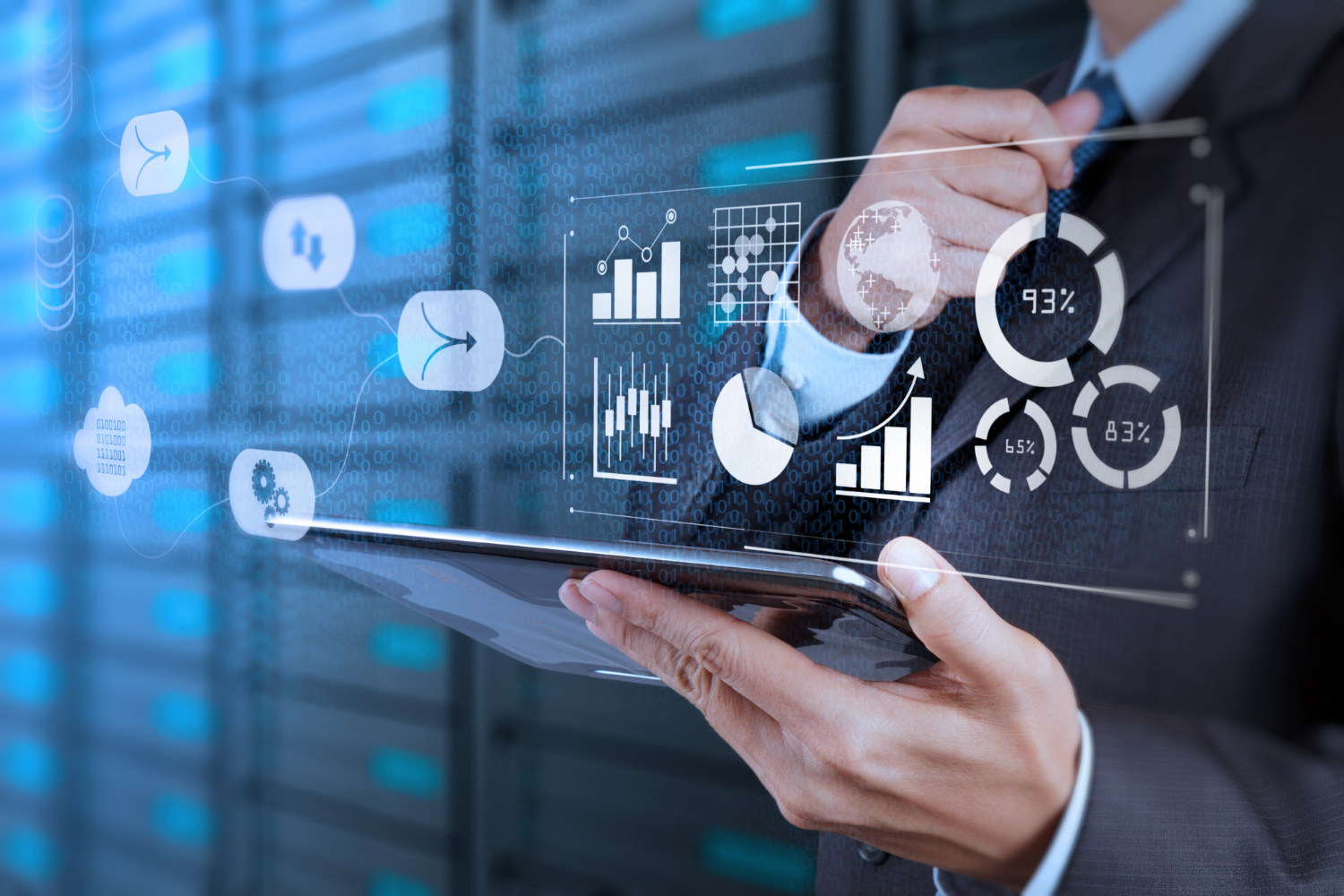
What is SAP EWM?
SAP EWM is an advanced warehouse management system designed to manage complex logistics processes in warehouses and distribution centers. It extends the capabilities of traditional Warehouse Management Systems (WMS) by integrating with other SAP modules and offering features like advanced picking, labor management, and detailed analytics.
The Inbound Process
This step is crucial for maintaining the smooth operation of a warehouse. It encompasses all activities related to receiving goods into the warehouse, ensuring they are stored efficiently and accurately for future retrieval. Effective inbound processes help in minimizing delays, reducing errors, and ensuring that inventory records are up to date.
Breaking Down the Basic Inbound Process
1. Purchase Order
The inbound process begins with the creation of a Purchase Order (PO). This formal document specifies the details of goods or services to be purchased from a vendor, including quantities, prices, and delivery terms. The PO serves as a contract between the purchasing organization and the vendor, ensuring clarity and agreement on the transaction details.
2. Inbound Delivery in the ERP
Once the PO is created, the next step involves generating an inbound delivery document in the ERP system (such as SAP ECC or S4HANA). This document contains crucial information about the expected goods, such as delivery dates, quantities, and vendor details. It acts as a notification to the warehouse about incoming shipments, allowing them to prepare for receipt.
3. Inbound Delivery in EWM
The inbound delivery is then transferred to SAP EWM, where additional warehouse-specific information is added. This includes storage bin assignments, handling units, and warehouse tasks. This step ensures that the warehouse management system has all the necessary details to manage the receipt and storage of the goods effectively.
4. Posting of Goods Receipt
Upon the arrival of goods at the warehouse, the goods receipt is posted in the system. This step involves confirming the arrival of the goods, updating inventory records, and ensuring that the quantities received match those specified in the purchase order. Posting the goods receipt is crucial for maintaining accurate inventory levels and financial records.
5. Storage of the Goods
The final step in the inbound process is the actual storage of the received goods in designated locations within the warehouse. The goods are brought to their assigned storage bins, ensuring they are organized and accessible for future use. Proper storage practices are essential for optimizing space utilization and facilitating efficient retrieval during the outbound process.
Is it suitable for everyone?
While the basic process flow for inbound logistics is straightforward, real-world scenarios often require customization to address specific business needs. Intermediate steps, such as quality inspections, cross-docking, and value-added services, may need to be integrated into the standard process flow. In the next article of this series, we show you how this can be achieved.